Common Solid Axle Failures and How to Prevent Them
Prevent axle failures by maintaining bearings, seals, U-joints, and differentials. Regular inspections, lubrication, and proper load management extend component life.
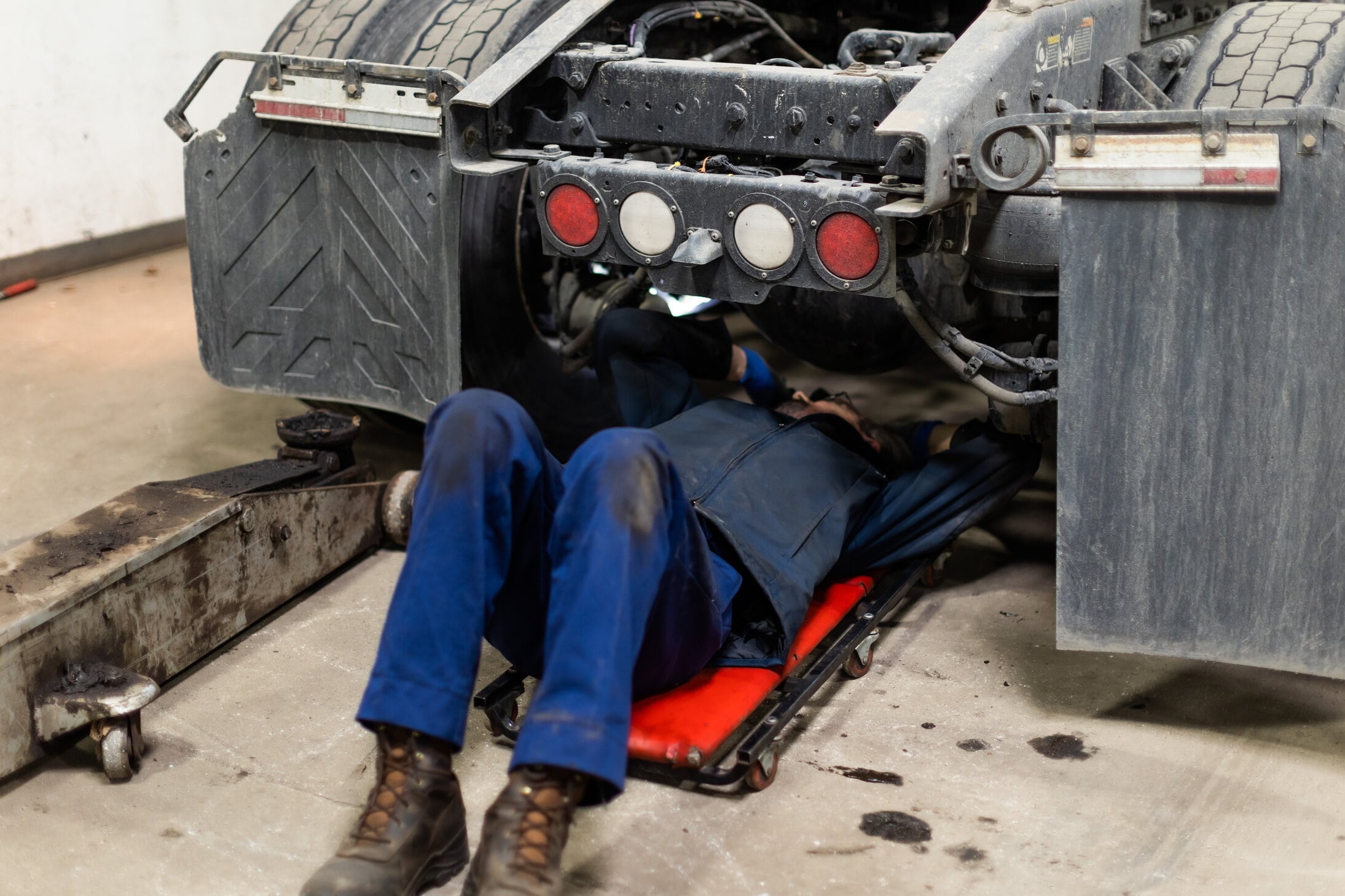
Solid axles are built to handle extreme loads, rugged terrain, and the high torque output of diesel engines. They are commonly used in heavy-duty trucks, off-road vehicles, and commercial fleets because of their strength and durability. However, they are not immune to wear and tear. Over time, heavy use and poor maintenance can lead to serious failures, resulting in costly repairs, vehicle downtime, and even safety hazards.
This article will explore the most common solid axle failures, their causes, and practical steps to prevent them. Proper maintenance and early detection of problems can significantly extend the life of your truck’s solid axle and prevent expensive repairs down the road.
1. Bearing Failure: The Silent Destroyer
The Problem
Axle bearings reduce friction between the axle shaft and the wheel hub, allowing smooth rotation under heavy loads. Over time, these bearings can wear out due to:
- Lack of lubrication
- Water or dirt contamination
- Overloading beyond the axle’s weight rating
- Excessive heat buildup
When axle bearings fail, they create excessive friction, overheating, and metal-on-metal grinding. If left unchecked, a failed bearing can seize up, causing the wheel to lock or detach from the axle.
Prevention Tips
- Regular Inspections: Listen for unusual noises such as grinding, humming, or whining from the wheels. These are often the first signs of a failing bearing.
- Proper Lubrication: Use high-quality grease specifically designed for heavy-duty bearings. Ensure that all bearings are properly packed during routine maintenance.
- Monitor Load Limits: Avoid exceeding your truck’s Gross Axle Weight Rating (GAWR), as excessive loads can put undue stress on the bearings.
- Protect Against Contaminants: Water and dirt infiltration can cause premature bearing wear. Check seals for damage and avoid deep water crossings without proper protection.
2. Bent or Broken Axle Shafts
The Problem
Axle shafts are designed to transfer power from the differential to the wheels. These components endure enormous stress, especially in heavy-duty applications such as towing, hauling, and off-road driving. Axle shafts can bend or break due to:
- Excessive load weight
- Hard impacts from potholes, curbs, or rough terrain
- Metal fatigue from prolonged use
- Improperly installed aftermarket modifications
A bent or broken axle shaft can cause vibration, wobbling, and uneven tire wear. It can lead to total drivetrain failure in severe cases, rendering the truck inoperable.
Prevention Tips
- Avoid Aggressive Driving: Sudden torque surges and aggressive acceleration can overstress the axle shaft, especially when towing or carrying heavy loads.
- Inspect Axles After Off-Road Use: Regularly check for visible bends, cracks, or unusual wear on the axle shafts.
- Upgrade to Heavy-Duty Axles: If your truck frequently handles extreme loads or off-road conditions, consider reinforced axle shafts made of high-strength alloys.
- Steer Clear of Deep Potholes and Obstacles: Hard impacts can weaken the axle over time. Whenever possible, drive cautiously over rough terrain.
3. Differential Wear and Damage
The Problem
The differential is a critical component of the solid axle, allowing the wheels to rotate at different speeds while maintaining traction. Over time, the gears inside the differential can wear down due to:
- Low or contaminated differential fluid
- Worn-out bearings inside the differential housing
- High torque loads without proper reinforcement
- Leaking seals leading to lubrication failure
If the differential begins to fail, you may experience symptoms such as clunking or grinding noises, difficulty turning, or fluid leaks around the differential housing. In severe cases, differential failure can leave your truck unable to move.
Prevention Tips
- Change Differential Fluid Regularly: Old, dirty fluid can cause premature gear wear. Follow the manufacturer’s recommendations for service intervals and use high-quality gear oil.
- Check for Leaks: Look for signs of fluid leaks around the differential housing. If a leak is found, replace the seals promptly to prevent further damage.
- Upgrade the Differential Cover: Some stock covers flex under load, leading to misalignment of the gears. Aftermarket reinforced covers provide extra protection and better heat dissipation.
- Monitor for Unusual Noises: Clicking, grinding, or excessive whining sounds from the rear axle can indicate early differential wear. Address issues early to prevent costly repairs.
4. U-Joint and Yoke Failures
The Problem
Universal joints (U-joints) and yokes connect the driveshaft to the axle, allowing flexibility in the drivetrain. These components are prone to failure due to:
- Lack of lubrication
- Corrosion from exposure to water and road salt
- Misalignment of the driveshaft
- Excessive load stress
A failing U-joint can cause clunking sounds, vibrations, and even complete drivetrain failure if the driveshaft disconnects from the axle.
Prevention Tips
- Grease U-Joints Regularly: Use heavy-duty grease during routine maintenance to prevent premature wear.
- Check for Excessive Play: Any looseness in the U-joints or yoke is a sign of wear and should be addressed immediately.
- Upgrade to Heavy-Duty U-Joints: If your truck operates under high torque loads, consider forged U-joints for extra durability.
5. Axle Seal Leaks
The Problem
Axle seals prevent differential fluid from leaking out and contaminants from entering the axle housing. Over time, seals can deteriorate due to:
- Age and exposure to heat
- Improper installation
- Excessive off-road driving or impact damage
Leaking seals can lead to low differential fluid levels, increased heat, and eventual gear failure.
Prevention Tips
- Inspect Seals During Oil Changes: Look for fluid around the wheel hubs or differential housing. Replace worn or leaking seals immediately.
- Use High-Quality Replacement Seals: Choose OEM or high-quality aftermarket seals for better longevity.
- Avoid Power Washing the Axle Ends: High-pressure washing can force contaminants past the seals, leading to premature failure.
6. Suspension Stress on Solid Axles
The Problem
Solid axles rely on leaf springs or air suspension to distribute weight and absorb road impacts. Worn-out suspension components can cause excessive stress on the axle, leading to premature wear and alignment issues.
Prevention Tips
- Inspect Suspension Components Regularly: Look for cracked leaf springs, worn-out bushings, or sagging airbags.
- Upgrade Suspension for Heavy Loads: Progressive-rate leaf springs or heavy-duty air suspension can improve durability and ride quality.
- Ensure Proper Alignment: Misaligned axles increase tire wear and strain suspension components unnecessarily.
Final Thoughts: Keep Your Solid Axle in Peak Condition
A well-maintained solid axle can provide years of reliable service, even under extreme conditions. Regular inspections, proper lubrication, and timely upgrades are essential for preventing failures and extending the lifespan of your truck’s drivetrain.
At Rapid Tire & Alignment in Rapid City, SD, we specialize in solid axle maintenance, repairs, and upgrades for heavy-duty diesel trucks. If you notice vibrations, leaking seals, or unusual noises from your axle, don’t wait—bring your vehicle in for an inspection today.